Technology
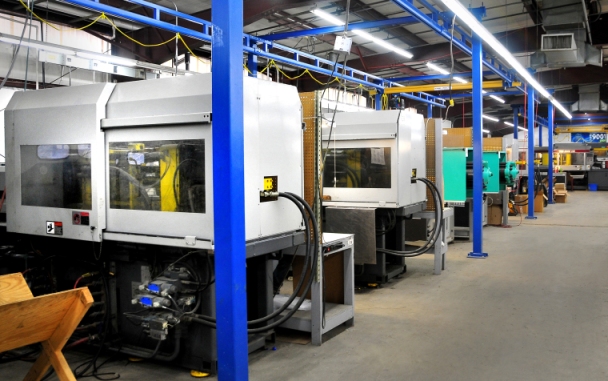
At United Industries, technology is a means to the end. Everyone in the organization is empowered to use technology based on the value it brings our customers. We use state-of-the-art machines that help us stay efficient and effective. Our operators are well-trained in both usage and maintenance of machines. They’re also encouraged to continuously upgrade their skills.
Machines make life easy. Machines still need human intervention to carry out their tasks. What if machines could talk back and tell the human operators if they are facing some problems?
United Industries is pioneering Industry 4.0 within the context of the South Indian plastic injection moulding space. Our vision is to use technology to create Smart Factories where machines communicate and cooperate with humans in real time. The primary benefit of this technology would be to offer internal and cross-organizational services that add value to customers.
Plastic injection moulding machines at United Industries are outfitted with visual indicator sensors that informs operators about the status of critical machine components. These indications enable timely action by the operator and ensure that the machine operates at it’s full capacity.
Technology need not always be complex and digital. Simple paper-based analog tools can also be effective in making manufacturing smoother.
United Industries has introduced Route Tags to track and monitor the status of moulded parts. Route Tags highlight the route that moulded parts need to take. They can either be “Waiting for Inspection”, “Waiting for Assembly” or land up as “Finished Goods (FG)”. Marking routes also helps estimate the time spent by parts in different areas.
Processses
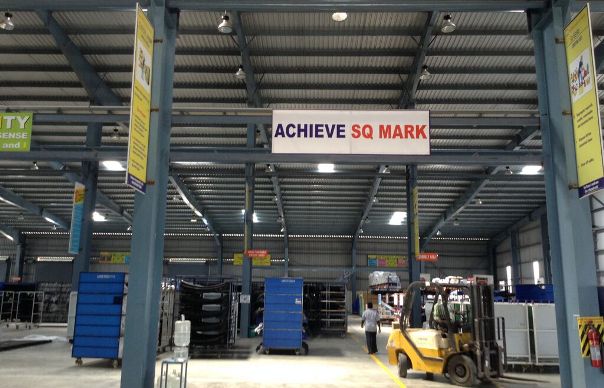
Processes help us get more clarity about our work. United Industries creates simple, structured processes to streamline information and make it visible to everyone. Right from the time a client approaches us, to the final shipment of moulded parts, our processes take charge and ensure high quality output.
United Industries uses Poka-Yoke, the Japanese method of systematic error-proofing across the organisation. Errors are inevitable in manufacturing environments. But, it is essential to catch these errors and initiate preventive measure to avoid defects at the source. Poka-Yoke has been implemented in various stages of the plastic injection moulding process to support the production of high-quality products for our customers.