Hanil Automotive
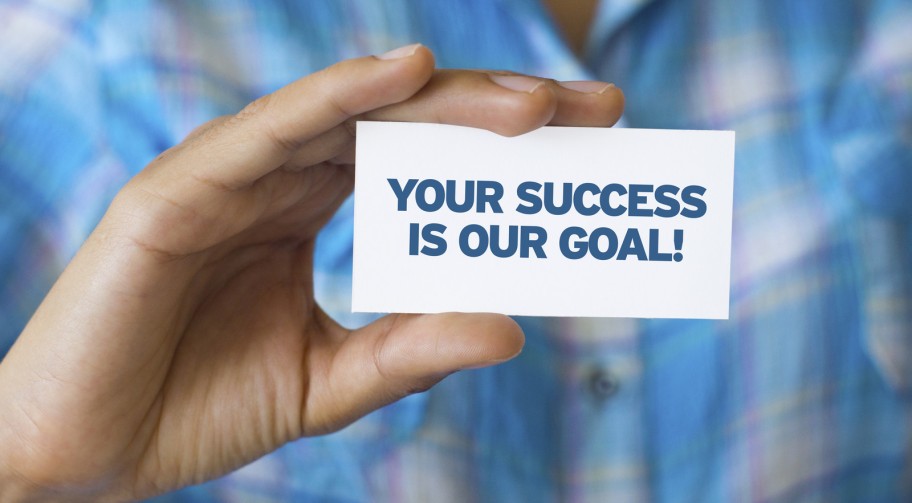
As Tier II suppliers to Hanil Automotive, our relationship is built on transparency and trust. One of the issues that they faced was excessive flush over the car surface for a certain part. This caused further trouble down the assembly line when other parts had to be assembled. Hanil Automotive contacted us to report the problem and United Industries promptly got down to work on it.
How was the issue received?
A team headed by a senior engineer was immediately assigned the task of handling this issue. The details of the problem including surrounding environmental data were captured along with HA and documented. Since this was a quality assurance topic, a quality problem countermeasure process was initiated.
How was the issue resolved?
The countermeasure team decided to split the issue and look for both temporary and permanent solutions. In parallel, a root cause analysis was also initiated to understand the problem and prevent it’s future occurrence.
As a temporary countermeasure, the parts were marked with a special identifier in order to track them during tolerance matching with the official checker part which is a 100% reproduction of the final part on the car surface. A quality alert was raised in all areas and UI associates were alerted to use the special part identifier to double—check the part for fit and tolerance. These actions were completed within 48hours of hearing about the problem from HA.
While the temporary countermeasures were being implemented, the root cause analysis revealed a few interesting results. A minor shrinkage was observed due to improper locking of the the retainer during the moulding process. On tracing this further down the line, the final root cause was revealed to be a blockage of the cooling line caused due to de-scaling within the mould.
Once the root cause was derived, a process modification was undertaken. Two major parameters were changed - the frequency of de-scaling and usage of the checker part. The moulds were to be checked more frequently for de-scaling and the parts were verified with the checker every 1 hour (compared to the earlier frequency of once every 4 hours). The process modification and all other actions that lead to a permanent resolution were completed within 10 days of receiving the issue.
All along the quality problem countermeasure process, Hanil Automotive was kept in the loop with regular updates informing them about the status and resolution measures. Eventually, the flush issue was successfully resolved and United Industries has continued working with Hanil Automotive to deliver high-quality solutions in plastic injection moulding.